Fitted the windscreen wipers, these have a 95 degree sweep, so I've mounted the offside one just to the right of the steering wheel center, and the other about 5" to the left of where the tip of the blade finishes. Finding the position was easier than I expected, using a protractor and the arms and some tape I put them in various positions and checked that the were not missing anything in my field of vision.
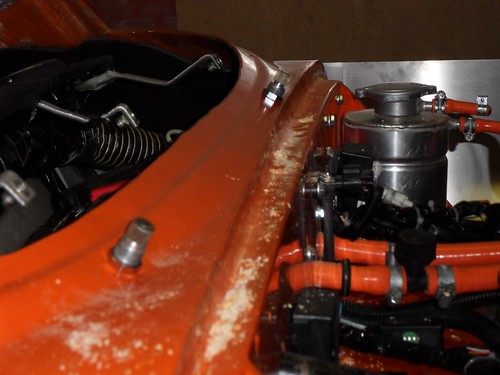
Fitting the wheel boxes to the motor on the other hand was endless frustration. The theory is simple enough, there is a corrugated flexible bit of wire that runs through some copper tube from the motor to the wheel boxes, the wheel in the wheel boxes is turned by the teeth on the wire, the wire is pushed and pulled by a crank on the end of the spindle.

I measured and cut the tube, and used a mandrel to bend it into the right shape, offered it up to the wire, and of course, it didn't go in. The wire is about 8mm, as is the ID of the copper tube. I de-burred the edge, and tried again and it got as far as the first bend, where of course it was too narrow to go any further. I spent a good few hours trying smaller radius bends, before finding another roll of ever so slightly larger tube that allowed at least some movement.
I then flared the end, before noticing that i hadn't put the nut on yet, after remedying that I offered up the rather inflexible assembly to the wheel box. This is located under the windscreen, above the electrical tray. It fits in there with a bit of bending, but removing the nuts on the end require the patience of job. These nuts are used to clamp the copper pipe in place, the wire then goes through the wheel box, and into another section of copper tube. I spent a good hour wiggling, and eventually managed to get the wire to pass over the lip on the clamp, another eternity tightening it up, before i (thankfully) had the good wisdom to test it worked, because as soon as i pressed the button the fuse popped. Tried again with a slightly larger fuse, and it pushed the flare out the motor end, i yanked on the wire and it was locked solid.
I assumed this was down to the cable being crushed, but after removing it, it was obvious that you have to thread the wire through the wheel box, as there is not enough of a gap for it to sit home if you don't, so basically when i tightened up the clamp i was just locking the wire in place.
I decided at this point, that things were getting too complicated, so i decided to use 10mm ally tube, and move the motor inside the car to eliminate the need for tight bends in the tube, this should allow the mechanism to run smoothly as well as making it easier to fit.
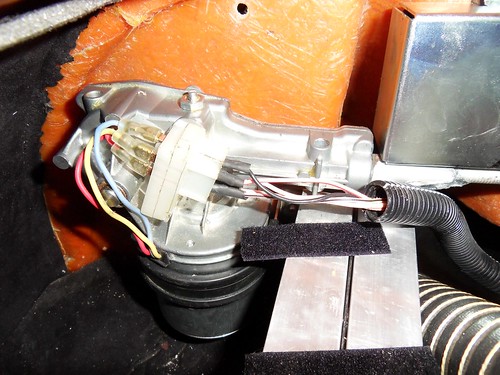
I drilled out the brass nut on the motor to 10mm, and put a flare on the tube, put the nut in a vice and screwed in an alloy boss which sits in the motor housing and is clamped in place by the cover of the motor. Of course i over tightened it and it sheered away in my hand. This was turning into a bit of a bodge, so after a bite to eat, i decided the best option was to make a new boss. (its simply a T shaped bit of metal with a hole in it) I did this by taking some alloy bar, turning it down so it had a lip on it. I then brazed the alloy tube to it using durafix, and some air of professionalism started to return to the finished result.
With it all bolt in place, the mechanism moves very smoothly, and is rock solid, which was pretty much what I wanted. I can now keep myself awake when i sit in the car by being slapped in the face by the wiper arm until I get round to sorting out a windscreen.

Next job was to fit the intercom. I've mounted it on the sidepod to my right, just at the end of my arms reach under the dash, to make the wiring tidier, i drilled a series of holes in the back of the casing and routed the power, and comms wires out there, leaving just the inputs for the music/gps etc at the front. The wires for the headsets will run along the outside of the sidepod to their rubber mounts.

The side repeaters are also fitted and wired up, along with an indicator switch and working hazard switch (Using a conventional way of doing things.) which will do until SVA, although for some reason my flasher wont flash, i tried a different flasher, and it flashes, but at the wrong rate due the LED lights, so i've ordered a replacement LED flasher unit.
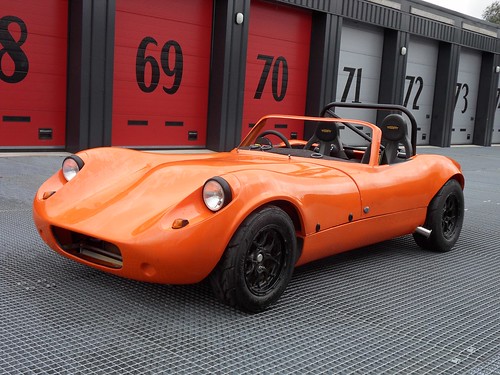
I made a very crude, and tbh not very good shift lever by extending a momentary on toggle switch with some alloy tube, this will do until I get rid of the ginormous sierra steering wheel (Post IVA) and can fit a proper flappy panel wotsit behind the smaller momo one.