I'm pretty sure I don't need to take the prop shafts out now, so today I fitted the bolts for a final time. This is something you want to get right, as the prop shafts turn at very high rpm. If they come off, the end that comes off will flay around. This is a bad thing. Sometimes its just a case of new panels, other times it can sever the fuel lines causing the car to
catch fire or if it breaches the floor, the car could be jacked up, causing it to rollover, or if it breaches the panelling into the cockpit it can cause injury to me or a passenger.
Bike engines produce a lot of vibrations and this has a habit of causing things to loosen off. In addition, there are two prop shafts, and a sprocket adapter which is three times as many things to fall off as on the seven.
My plan therefore is to use three things to stop the bolts coming off:
- Tighten the bolts RFT.
- Use threadlock on all bolts
- Use lockwire or a locking tab on all bolts.
The sprocket adapter bolt is a tricky one, as it is enclosed by the prop and the adapter, this is tightened to 86nm, with locktite, and it has a locking tab which i've hammered down. The problem is however, that I cannot see this bolt visually to check periodically. What I will do initially is retighten it after 100 miles, if it is loose then it will just have to be done regularly or i'll drill a hole in the adapter and lockwire it. To give me an indication of any movement, I've put a line of paint at the joint, if the bolt is coming loose there will be a gap (however small) betwen the line of paint and the adapter which should give an early indication. The bolts are M8 cap head grade 12, and are tightened as tight as I can get them, threadlocked, lockwired, and marked.
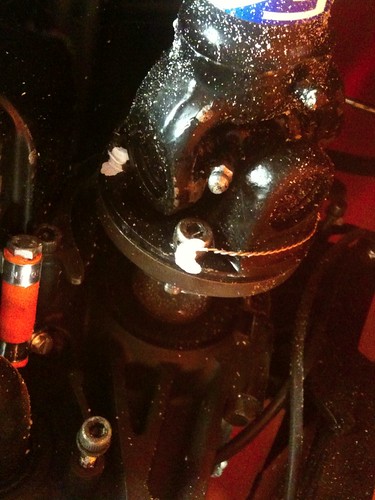
The reversing box uses M8 bolts, these are grade 12, and tightened as tight as I can get them with the spanner, again threadlocked. These are lockwired in pairs and marked with paint.

The rear flange uses nuts and bolts, again grade 12 bolts, with nylocs and threadlock. I've lockwired the bolts and used a locking tab on the rear which is bent over the nuts to stop them turning. Again they are tightened as tight as I can, and marked for security.